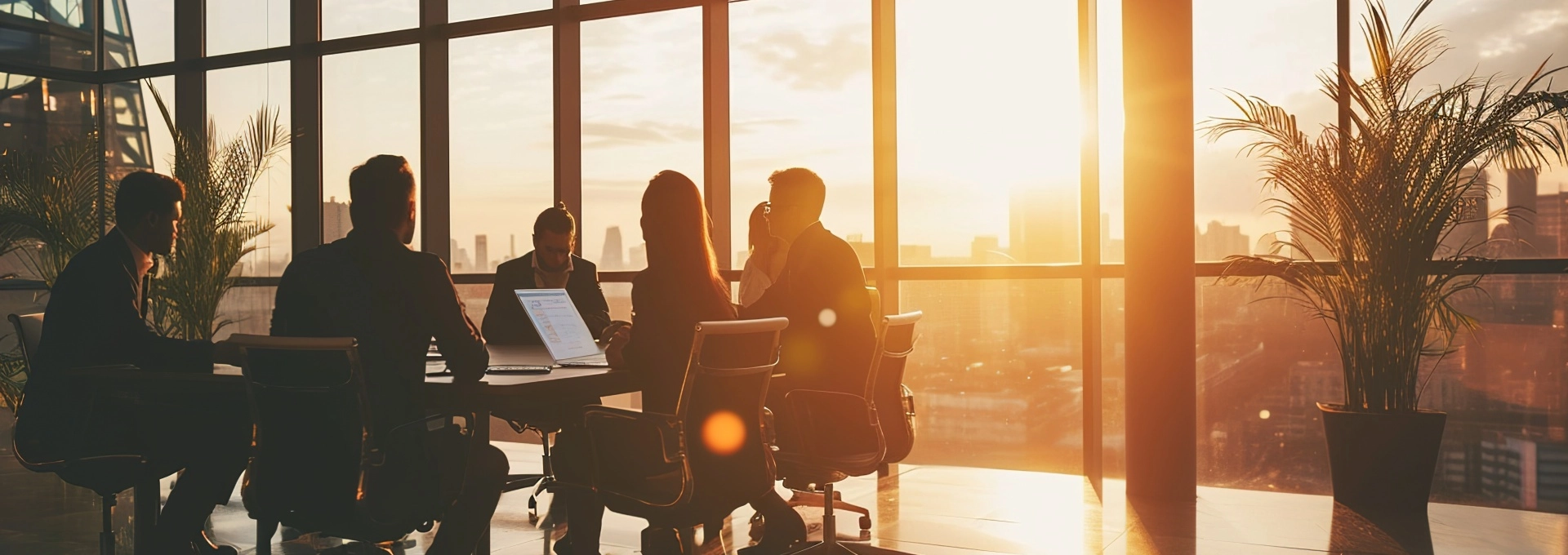
L'industrie traverse une période de transformation profonde, marquée par l'émergence de technologies révolutionnaires. Ces avancées techniques offrent aux entreprises manufacturières des opportunités inédites pour accroître leur productivité, leur qualité et leur compétitivité. L'adoption de solutions innovantes comme l'intelligence artificielle, l'Internet des objets industriel ou encore la réalité augmentée permet d'optimiser les processus de production, de réduire les coûts et d'améliorer la performance globale des usines. Cet article présente des conseils concrets pour tirer pleinement parti de ces technologies de pointe et moderniser efficacement son outil industriel. Les entreprises qui sauront implémenter ces innovations seront les mieux armées pour prospérer dans un environnement économique en constante évolution.
Optimisez vos processus de production industrielle
L'optimisation des processus de production constitue un levier majeur de compétitivité pour les industries manufacturières. Elle permet d'accroître la productivité, de réduire les coûts et d'améliorer la qualité des produits finis. Plusieurs axes d'amélioration peuvent être explorés pour rendre les chaînes de production plus performantes et agiles. Novae-group.com propose des solutions pour accompagner cette transformation numérique.
Réduisez les temps d'arrêt machines
La réduction des temps d'arrêt non planifiés des équipements de production représente un enjeu crucial pour maximiser le taux d'utilisation des lignes. L'installation de capteurs connectés sur les machines permet de collecter en temps réel des données sur leur fonctionnement et leur état. L'analyse de ces informations à l'aide d'algorithmes d'intelligence artificielle permet de détecter de manière précoce les signes avant-coureurs de défaillances. Les équipes de maintenance peuvent ainsi intervenir de façon préventive avant qu'une panne ne survienne et n'entraîne un arrêt de production coûteux. Les temps d'arrêt peuvent être réduits de 30 à 50% grâce à ces technologies prédictives. La mise en place d'une maintenance conditionnelle basée sur l'état réel des équipements, plutôt que sur des intervalles fixes, optimise également la disponibilité des machines tout en réduisant les coûts de maintenance.
Améliorez le contrôle qualité produits
L'amélioration du contrôle qualité des produits manufacturés passe par l'utilisation de technologies avancées d'inspection et d'analyse. Les systèmes de vision industrielle couplés à des algorithmes d'intelligence artificielle permettent de détecter automatiquement les défauts sur les pièces produites, avec une précision et une rapidité bien supérieures aux contrôles manuels. Ces solutions peuvent identifier des défauts minimes invisibles à l'œil nu et assurer un contrôle à 100% de la production. L'analyse des données collectées permet d'identifier les causes racines des problèmes qualité et d'optimiser les processus en amont. La mise en place d'un suivi qualité en temps réel sur toute la chaîne de production permet de réagir rapidement en cas de dérive et d'éviter la production de séries défectueuses coûteuses.
Automatisez les tâches répétitives manuelles
L'automatisation des tâches répétitives et à faible valeur ajoutée permet d'accroître la productivité tout en réduisant la pénibilité pour les opérateurs. Les cobots, ou robots collaboratifs, offrent de nouvelles possibilités pour automatiser des opérations manuelles tout en conservant la flexibilité nécessaire. Contrairement aux robots industriels traditionnels, ils peuvent travailler aux côtés des humains sans barrière de sécurité. Leur programmation simplifiée permet de les déployer rapidement sur différentes tâches. L'automatisation des opérations de manutention, d'assemblage ou de conditionnement permet de réduire les temps de cycle et d'améliorer la régularité de la production. Les véhicules à guidage automatique (AGV) optimisent quant à eux les flux logistiques internes à l'usine. L'automatisation libère les opérateurs des tâches répétitives pour se concentrer sur des activités à plus forte valeur ajoutée.
Implémentez l'intelligence artificielle dans votre usine
L'intelligence artificielle (IA) offre des perspectives révolutionnaires pour optimiser les processus industriels et accroître la compétitivité des usines. Son déploiement permet d'exploiter pleinement la masse de données générées par les capteurs et systèmes connectés pour prendre des décisions plus rapides et pertinentes. Les algorithmes d'apprentissage automatique sont capables d'analyser en temps réel des millions de paramètres pour détecter des schémas complexes invisibles à l'œil humain. L'IA peut ainsi être utilisée pour optimiser la planification de la production, prédire les pannes machines, détecter les défauts qualité ou encore réduire la consommation énergétique. Son implémentation nécessite une approche progressive, en commençant par des projets pilotes ciblés avant un déploiement à plus grande échelle. La collecte et la centralisation des données industrielles constituent un prérequis essentiel. La mise en place d'une plateforme IIoT (Industrial Internet of Things) permet d'agréger les données provenant des différents équipements et systèmes. Ces données sont ensuite exploitées par des modèles d'IA entraînés sur les spécificités de chaque processus industriel. L'IA permet également d'automatiser certaines tâches cognitives comme l'inspection qualité visuelle ou l'optimisation des paramètres machines. Ci-dessous, vous trouverez les éléments essentiels :
Application de l'IA | Bénéfices potentiels |
---|---|
Maintenance prédictive | Réduction de 30-50% des temps d'arrêt |
Optimisation de la production | Augmentation de 20-30% de la productivité |
Contrôle qualité automatisé | Détection de 99,9% des défauts |
Maîtrisez la maintenance prédictive des équipements
La maintenance prédictive constitue un levier majeur pour optimiser la disponibilité des équipements industriels tout en réduisant les coûts de maintenance. Cette approche s'appuie sur l'analyse en temps réel de l'état de santé des machines pour anticiper les défaillances avant qu'elles ne surviennent. Elle permet ainsi de passer d'une maintenance réactive ou préventive systématique à une maintenance conditionnelle basée sur l'état réel des équipements.
Surveillez l'état de santé machines
La surveillance en continu de l'état de santé des équipements repose sur l'installation de capteurs connectés mesurant différents paramètres comme les vibrations, la température, la pression ou encore la consommation électrique. Ces capteurs transmettent en temps réel les données collectées vers une plateforme centralisée via des réseaux sans fil industriels. L'analyse de ces données permet de détecter des dérives subtiles dans le comportement des machines, invisibles à l'œil nu. Des algorithmes d'intelligence artificielle comparent en permanence les mesures aux valeurs nominales pour chaque équipement. Ils sont capables d'identifier des tendances ou des schémas anormaux pouvant indiquer une dégradation progressive. Cette surveillance constante permet d'avoir une visibilité précise sur l'état de chaque machine et d'optimiser les interventions de maintenance.
Anticipez les pannes avant qu'elles surviennent
L'anticipation des pannes avant qu'elles ne se produisent constitue l'objectif principal de la maintenance prédictive. Les modèles prédictifs basés sur l'apprentissage automatique analysent l'historique des données de fonctionnement et de maintenance pour identifier les signes précurseurs de défaillances. Ils peuvent ainsi prédire avec plusieurs semaines d'avance la probabilité qu'un composant tombe en panne. Ces prévisions permettent de planifier les interventions au moment optimal, ni trop tôt ni trop tard. Les pièces de rechange peuvent être commandées et les ressources allouées en conséquence. Les temps d'arrêt non planifiés sont ainsi considérablement réduits, tout comme les coûts liés aux pannes. La maintenance prédictive permet également d'optimiser la durée de vie des composants en les remplaçant au bon moment.
Optimisez les interventions maintenance préventive
L'optimisation des interventions de maintenance préventive s'appuie sur une connaissance fine de l'état réel de chaque équipement. Les plans de maintenance peuvent être ajustés dynamiquement en fonction de l'usure effective des composants plutôt que sur des intervalles fixes. Les opérations sont ainsi effectuées uniquement lorsqu'elles sont réellement nécessaires, évitant les remplacements prématurés de pièces. La priorisation des interventions se fait en fonction de la criticité des équipements et de leur impact potentiel sur la production. Les ressources de maintenance sont ainsi allouées de manière optimale. La planification intelligente des interventions permet également de les regrouper pour minimiser les perturbations sur la production. L'analyse des données historiques permet d'identifier les meilleures pratiques et d'optimiser en continu les procédures de maintenance.
Misez sur la réalité augmentée industrielle
La réalité augmentée (RA) offre de nouvelles perspectives pour améliorer l'efficacité et la sécurité des opérations industrielles. Cette technologie superpose des informations virtuelles au monde réel via des lunettes connectées ou des tablettes. Elle trouve de multiples applications dans l'industrie, de la formation des opérateurs à la maintenance des équipements. La RA permet notamment de guider visuellement les techniciens lors des opérations de maintenance complexes. Des instructions étape par étape sont superposées directement sur les équipements, réduisant les risques d'erreur et accélérant les interventions. Les opérateurs peuvent également visualiser en temps réel des informations contextuelles sur les machines, comme les paramètres de production ou les alertes. La RA facilite aussi la collaboration à distance entre experts et techniciens sur le terrain. Un expert peut ainsi guider visuellement un technicien à distance comme s'il était sur place. La formation des nouveaux employés est également facilitée grâce à des simulations en réalité augmentée reproduisant fidèlement l'environnement de travail. La RA trouve aussi des applications dans le contrôle qualité, en superposant par exemple le modèle 3D théorique à la pièce réelle pour détecter les écarts. Les points clés à retenir sont :
- Guidage visuel des opérations de maintenance
- Visualisation en temps réel des données machines
- Collaboration à distance entre experts
- Formation immersive des opérateurs
- Contrôle qualité assisté par RA
Sécurisez vos données industrielles sensibles critiques
La sécurisation des données industrielles sensibles constitue un enjeu majeur à l'heure de l'usine connectée. La multiplication des capteurs et systèmes connectés accroît la surface d'attaque potentielle pour les cybercriminels. Une compromission des systèmes industriels peut avoir des conséquences dramatiques, allant de l'arrêt de production au vol de secrets industriels. La mise en place d'une stratégie de cybersécurité robuste est donc indispensable. Celle-ci doit couvrir l'ensemble des couches du système d'information industriel, des capteurs terrain jusqu'aux applications métier. La segmentation du réseau permet d'isoler les systèmes critiques et de limiter la propagation d'éventuelles attaques. Le chiffrement des communications est essentiel pour protéger les données sensibles transitant sur les réseaux. L'authentification forte des utilisateurs et des équipements limite les risques d'intrusion. La surveillance en temps réel du trafic réseau permet de détecter rapidement les comportements anormaux. Des sauvegardes régulières et sécurisées sont indispensables pour assurer la continuité d'activité en cas d'incident. La sensibilisation et la formation des employés aux bonnes pratiques de cybersécurité sont également cruciales. Une veille active sur les nouvelles menaces et vulnérabilités permet d'adapter en permanence les dispositifs de protection.